ERP for Manufacturing: Streamlining Operations and Boosting Efficiency
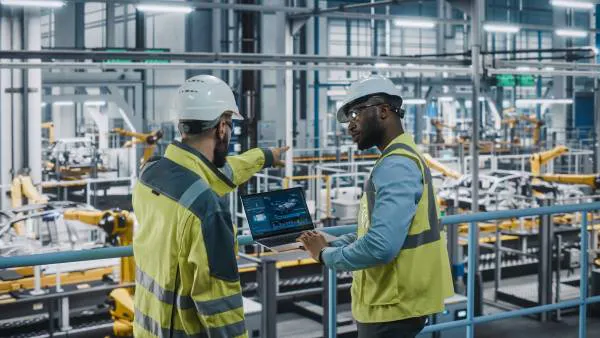
In the fast-paced world of manufacturing, staying competitive requires more than just advanced machinery and skilled labor. The ability to manage resources, streamline processes, and maintain real-time visibility into every aspect of operations is crucial. This is where Enterprise Resource Planning (ERP) systems come into play. ERP for manufacturing (Opens in a new window) is designed to integrate various functions across an organization, from production and inventory management to finance and human resources, into a single, unified system. This article explores the benefits of ERP systems in manufacturing, the key features to look for, and how they can transform your business.
1. Understanding ERP for Manufacturing
Enterprise Resource Planning (ERP) systems are comprehensive software platforms that manage and integrate the core business processes of an organization. In the context of manufacturing, ERP systems are tailored to meet the unique challenges of the industry, such as production planning, supply chain management, and quality control. By consolidating data from different departments into one central database, an ERP system ensures that everyone in the organization has access to accurate, real-time information.
ERP for manufacturing is not just about managing day-to-day operations; it's about creating a more efficient, agile, and responsive business. It provides manufacturers with the tools they need to optimize production schedules, reduce waste, improve product quality, and enhance customer satisfaction.
2. Key Benefits of ERP in Manufacturing
Implementing an ERP system in a manufacturing environment offers numerous benefits that can significantly impact the bottom line. Some of the key advantages include:
Improved Efficiency: ERP systems automate many manual processes, reducing the time and effort required to complete tasks. This leads to faster decision-making and a more streamlined workflow.
Enhanced Production Planning: With real-time data on inventory levels, machine availability, and labor resources, manufacturers can create more accurate production schedules. This minimizes downtime and ensures that production runs smoothly.
Better Inventory Management: ERP systems provide visibility into inventory levels across the supply chain, helping manufacturers avoid stockouts and overstock situations. This leads to better inventory control and cost savings.
Quality Control: ERP systems include tools for tracking and managing quality throughout the production process. This ensures that products meet the required standards and reduces the risk of defects.
Real-Time Reporting: With an ERP system, manufacturers can generate real-time reports on key performance indicators (KPIs) such as production efficiency, order fulfillment rates, and financial performance. This helps in making informed decisions and identifying areas for improvement.
Improved Collaboration: By providing a single source of truth for all departments, ERP systems facilitate better communication and collaboration within the organization. This leads to more cohesive and coordinated operations.
Regulatory Compliance: ERP systems help manufacturers stay compliant with industry regulations by tracking and documenting every aspect of the production process. This is particularly important in industries with strict regulatory requirements, such as pharmaceuticals or aerospace.
3. Key Features of ERP for Manufacturing
When choosing an ERP for Manufacturing business, it’s essential to look for features that align with your specific needs. Here are some of the critical features to consider:
Production Planning and Scheduling: The ERP system should offer tools for creating detailed production plans and schedules based on real-time data. This helps ensure that production runs efficiently and meets customer demand.
Inventory Management: An effective ERP system should provide comprehensive inventory management capabilities, including real-time tracking of raw materials, work-in-progress, and finished goods.
Supply Chain Management: The ERP system should integrate with your suppliers and distributors, providing visibility into the entire supply chain. This helps in managing procurement, reducing lead times, and optimizing logistics.
Quality Management: Look for an ERP system with robust quality management features, such as inspection planning, non-conformance tracking, and corrective action management. This ensures that your products meet the required quality standards.
Financial Management: The ERP system should include financial management tools that allow you to track costs, manage budgets, and generate financial reports. This helps in maintaining profitability and making strategic financial decisions.
Human Resources Management: An ERP system with integrated HR features can help manage employee data, track labor costs, and ensure compliance with labor laws. This is particularly important in manufacturing environments with large workforces.
Customer Relationship Management (CRM): A CRM module integrated into the ERP system helps manufacturers manage customer relationships, track orders, and ensure timely delivery. This leads to better customer satisfaction and repeat business.
Maintenance Management: In a manufacturing environment, maintaining equipment is critical to ensuring continuous production. An ERP system should include maintenance management features that track equipment usage, schedule preventive maintenance, and manage repair activities.
4. Implementing ERP for Manufacturing: Best Practices
Successfully implementing an ERP for Manufacturing environment requires careful planning and execution. Here are some best practices to ensure a smooth transition:
Define Clear Objectives: Before implementing an ERP system, it’s essential to define clear objectives that align with your business goals. This could include improving production efficiency, reducing costs, or enhancing customer satisfaction.
Choose the Right System: Not all ERP systems are created equal, and it’s crucial to choose one that meets the specific needs of your manufacturing business. Consider factors such as scalability, ease of use, and the ability to integrate with existing systems.
Involve Key Stakeholders: Involving key stakeholders from across the organization in the selection and implementation process is critical. This ensures that the system meets the needs of all departments and that everyone is on board with the change.
Plan for Change Management: Implementing an ERP system is a significant change for any organization, and it’s essential to have a plan in place for managing this change. This includes training employees, communicating the benefits of the system, and addressing any concerns.
Test and Validate: Before going live with the ERP system, it’s essential to thoroughly test and validate it to ensure it meets your requirements. This includes testing the system’s functionality, data accuracy, and integration with other systems.
Monitor and Optimize: Once the ERP system is live, it’s crucial to continuously monitor its performance and make any necessary adjustments. This includes tracking key performance indicators (KPIs), gathering feedback from users, and making improvements as needed.
5. Conclusion
ERP for Manufacturing looking to streamline their operations, improve efficiency, and stay competitive in a rapidly changing industry. By integrating all aspects of the business into a single, unified system, ERP allows manufacturers to make informed decisions, optimize processes, and enhance overall performance. Whether you’re a small manufacturer or a large enterprise, investing in the right ERP system can transform your business and set you on the path to long-term success.